
A company certified with ISO 9001 : 2015 standards.
Our Process
Rubber to Metal Bonding
Design & Application of Products
At Maurya Rubbers, we provide comprehensive design and application support to meet the unique needs of our customers. Whether you choose from thousands of existing products or require a custom-designed solution, we offer the expertise to bring your vision to life.
Our in-house Finite Element Analysis (FEA) not only
optimizes designs but also aids in product analysis, costings, weight analysis, and tool design. Through advanced tool design and development, we ensure that every product is manufactured with precision, meeting both functional and cost-effective requirements. Our specialized rubber formulation capabilities further enhance the performance and durability of each product. With our robust product development process, we ensure that your project moves smoothly from concept to full production, backed by the highest standards of quality.


Tooling development

At Maurya Rubbers, we understand that the quality of a product is directly influenced by the precision and efficiency of the tools used in its production. Our fully equipped in-house tool room allows us to design, develop, and maintain high-quality molds and tools for each of our manufacturing processes. This capability ensures that we can produce components with exceptional accuracy and reliability.
​
From the initial design stage to final tool creation, we utilize advanced software and techniques to develop customized tools tailored to specific product requirements. Our tool development process includes:
​
-
Design Optimization: Using advanced design and analysis tools, we ensure that the tools are optimized for both performance and cost efficiency.
-
Precision Tooling: Our in-house tool room is equipped to create precise, durable molds and dies, guaranteeing consistent product quality and dimensional accuracy.
-
Prototyping and Testing: We conduct thorough prototyping and testing to verify tool functionality and ensure it meets production standards.
-
Tool Maintenance and Upgrades: We ensure tools are regularly maintained and, when necessary, upgraded to keep pace with evolving product designs and production requirements.
​
By handling all aspects of tool development in-house, we reduce lead times, enhance product consistency, and maintain full control over the manufacturing process, ensuring superior results for every project.
Raw Rubber
Maurya Rubbers: Advanced Rubber Grades Manufacturing Capabilities
Maurya Rubbers specializes in manufacturing high-performance rubber products using a wide range of raw rubber grades, including:
​
-
Natural Rubber (NR)
-
Styrene-Butadiene Rubber (SBR)
-
Ethylene Propylene Diene Monomer (EPDM)
-
Nitrile Butadiene Rubber (NBR)
-
Chloroprene Rubber (CR)
-
Silicone Rubber (SI)
-
Fluoroelastomers (FKM)
-
Polyurethane Rubber (PU)
-
Butyl Rubber (IIR)
-
Acrylic Rubber (ACM)
​
We offer customized formulations and precision compounding, ensuring consistent, high-quality products for a wide range of industries, including automotive, industrial, and trailer manufacturing.
​

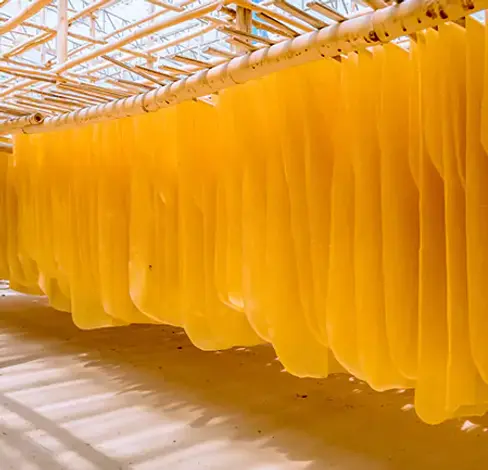
Rubber Compounding
At Maurya Rubbers, our rubber compounding process ensures the creation of high-performance materials tailored to meet specific application requirements.
​
Using advanced technology and precision mixing, we combine raw rubber grades with various additives, including fillers, curing agents, and plasticizers, to enhance the rubber’s strength, durability, flexibility, and other essential properties. Our state-of-the-art batch machines ensure accurate and consistent mixing, allowing for high-quality, custom formulations.
With in-house expertise and strict quality control, we optimize performance for automotive, industrial, and trailer applications, delivering reliable products for even the most demanding environments.
Calendering / Mixing
At Maurya Rubbers, we combine advanced mixing and calendering techniques to produce high-performance rubber products. Our rubber mixing process blends raw rubber grades with additives such as curing agents, fillers, and plasticizers, ensuring consistency and uniformity. Using state-of-the-art batch mixing machines, we achieve precise control over the material’s properties.
​
Following mixing, our calendaring process involves passing the rubber through a series of rollers to create thin, uniform sheets. This ensures consistent thickness and optimal texture for further processing. Together, mixing and calendering provide the foundation for high-quality, custom rubber products across automotive, industrial, and trailer applications.

Goods Receiving
At Maurya Rubbers, we prioritize the quality of our products by ensuring that only the finest raw materials are used in our manufacturing processes. All incoming raw materials, including rubber grades, fillers, curing agents, and additives, undergo thorough inspection and testing upon arrival. Our quality control team verifies that each material meets our strict specifications for consistency, performance, and reliability.
By rigorously assessing the quality of all incoming raw materials, we ensure that only top-grade materials are used, resulting in superior rubber products that meet the highest industry standards.

100% Testing of Rubber Batches
At Maurya Rubbers, we ensure the highest quality in every product by performing 100% testing on all rubber batches. Each batch undergoes rigorous testing to assess critical properties such as tensile strength, elongation, hardness, and resilience.
Our advanced testing equipment and in-house quality control team guarantee that every rubber batch meets strict standards for performance and durability. By conducting thorough, consistent testing, we ensure that each product is reliable and fully optimized for applications in automotive, industrial, and trailer manufacturing.


Metals Inspection
At Maurya Rubbers, we ensure the highest standards of quality by conducting thorough metal inspection processes for all components that involve metal-to-rubber bonding.
Incoming metals, such as steel, aluminum, and other alloys, are carefully inspected for purity, strength, and dimensional accuracy.
Our quality control team utilizes advanced testing techniques, including visual checks, dimensional measurements, and non-destructive testing methods, to verify that all metals meet stringent specifications.
This meticulous metal inspection ensures optimal performance, durability, and reliability in every rubber-to-metal bonded product we manufacture.
Metal turning and stamping
At Maurya Rubbers, we offer comprehensive metalworking services to support our rubber-to-metal bonding products.
​
-
In-House Metal Turning, Stamping, and Machining: We utilize advanced CNC turning, stamping, and machining capabilities to create high-precision metal components with tight tolerances. These in-house processes ensure custom metal parts are produced efficiently, meeting the specific requirements for rubber bonding applications.
-
Outsourced Metal Casting: For more complex and larger-volume components, we partner with trusted foundries for outsourced metal casting. This allows us to provide high-quality, intricate metal parts with excellent strength and dimensional accuracy, while maintaining cost-efficiency.
By combining in-house precision machining and outsourced casting, we ensure the consistent quality and reliability of every product, ideal for automotive, industrial, and trailer applications.
​​
​​​​​​​​​​​​​​​​​​​​​​​​​​​

​​​​​​​​Metal surface preparation
​​​
At Maurya Rubbers, we ensure superior bonding performance by meticulously preparing the surfaces of metal articles before rubber bonding. Our surface preparation process includes several key steps to optimize adhesion and ensure long-lasting durability:
​
-
Cleaning: We thoroughly clean metal surfaces to remove oils, dirt, rust, and contaminants that could interfere with bonding. This is done using advanced cleaning methods, such as chemical cleaning or abrasive blasting.
-
Surface Roughening: We employ techniques like grit blasting, sandblasting, or acid etching to create a roughened surface. This increases the surface area and promotes a stronger bond between the metal and rubber.
-
Priming: In some cases, we apply specialized primers that enhance the adhesion between the metal and rubber, ensuring a durable, high-strength bond.
By carefully controlling the surface preparation process, we ensure that every rubber-to-metal bonded product meets the highest standards of performance and reliability.​​​​​​​​​​​​​​​​​​​​​
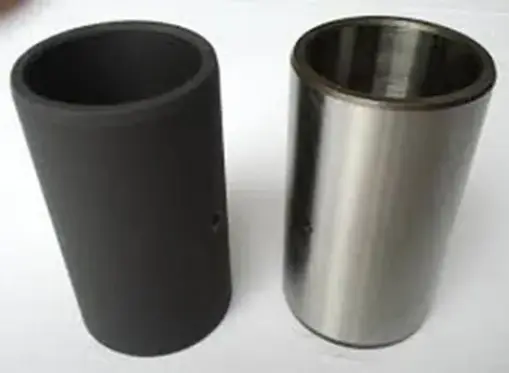

Vulcanisation
At Maurya Rubbers, vulcanization is a critical step in creating durable, high-performance rubber products. This chemical process involves cross-linking rubber molecules through the application of controlled heat, pressure, and curing agents, transforming raw rubber into a robust, elastic material with enhanced properties.
​
Our advanced vulcanization techniques ensure:
​
-
Superior Strength: Improved tensile strength and resistance to wear and tear.
-
Enhanced Durability: Increased resilience against environmental factors like heat, chemicals, and aging.
-
Precise Control: Uniform curing across all products, ensuring consistency and reliability.
-
​
This meticulous process is key to delivering rubber components suitable for demanding automotive, industrial, and trailer applications.
Test and verification
At Maurya Rubbers, we prioritize quality and reliability through an extensive testing and verification process at every stage of production. Our advanced testing capabilities include:
​
-
Material Testing: Assessing raw materials for properties such as tensile strength, hardness, and elasticity.
-
Dimensional Verification: Using precision measurement tools to ensure components meet exact specifications.
-
Performance Testing: Simulating real-world conditions to evaluate load-bearing capacity, vibration resistance, and durability.
-
Environmental Testing: Verifying resistance to heat, cold, moisture, and chemical exposure.
-
​
This rigorous testing framework ensures that our products meet stringent quality standards, delivering unmatched performance across automotive, industrial, and trailer applications.


Final inspection
Maurya Rubbers: Rigorous Final Inspection for Superior Quality
At Maurya Rubbers, we ensure every product meets the highest standards of quality through a meticulous final inspection process.
Each product undergoes comprehensive checks to verify dimensional accuracy, surface finish, and performance properties. Our inspection includes:
​
-
Visual Checks: Ensuring a flawless surface with no defects or irregularities.
-
Dimensional Accuracy: Precision measurements to confirm adherence to design specifications.
-
Performance Testing: Functional tests, such as load capacity, vibration damping, and bonding strength, to guarantee reliability under real-world conditions.
​
This rigorous process ensures every product leaving our facility is dependable, durable, and perfectly suited to its intended application.
At Maurya Rubbers, we ensure that every product reaches our customers in perfect condition through meticulous packaging and dispatch processes:
​
-
Custom Packaging Solutions: Products are packaged using high-quality materials tailored to their size, shape, and handling requirements, ensuring protection during transit.
-
Labeling and Identification: Each package is clearly labeled with detailed product information, batch numbers, and handling instructions for easy identification and tracking.
-
Quality Checks Before Dispatch: A final inspection is conducted to ensure all products meet customer specifications before shipment.
-
Timely and Reliable Shipping: Our efficient logistics team ensures prompt and secure delivery, minimizing lead times and maintaining customer satisfaction.
​
This end-to-end approach guarantees the safe and timely arrival of high-quality products to customers worldwide.
Packing and Despatch
